Comparison Between Cold/Hot Smart Water Flooding in Sandstone Reservoirs - Juniper Publishers
Juniper Publishers - Open Access Journal of Engineering Technology
Abstract
The incremental oil recovery has been investigated
and approved by many laboratory and field projects using water flooding
in tertiary stage. The salinity of the injected water is an important
factor observed by many researchers. The more salinity decreases the
more oil recovery obtained. The investigations on the hot low salinity
water flooding have been conducted by many researchers and they found
out that it is useful for increasing oil recovery especially heavy oil
due to reducing oil viscosity and make it easy to produce to the
surface. The thermal expansion of water plays an important role in the
incremental oil recovery mechanism, reducing the density of the injected
water relative to the aquifer water. This reduces mixing, minimizing
thermal loses to the aquifer.
Hot water flooding may also increase the economic
life of individual wells by as much as a factor of two. Smart water was
also used to alter the reservoir wettability and increase oil recovery
by manipulating the divalent cations in the injected water. In this
study, we used hot and cold smart water and injected both into the
sandstone saturated with crude oil in order to investigate the important
role of smart water itself and hot smart water. The systematic results
showed that changing some cations in the injected brines was better than
to spend more money to heat the smart water. The divalent cations Ca2+
and Mg2+ was the most effective component in the smart water. In this
study, we also studied the pH effect of the cold/hot smart water
effluent smart water EOR.
Keywords: Smart water
flooding; Sandstone reservoirs; Incremental oil recovery; Field
projects; Salinityinvestigations; Aquifer; Rod sucker pumpsIntroduction
Eastern Kansas oil fields contains heavy oil that is
produced via rod sucker pumps. The daily production fromBartlesville
Sandstone reservoir is around 500bbl/day with high water cut. Such
reservoirs have a low temperature and the oil viscosity of several
hundreds of centipoises. The mobility ratio is quite different between
the water and the heavy oil and if a conventional water flooding would
be conducted, the oil recovery could be low. A higher temperature of the
water flooding prompt to reduce the oil viscosity. The hot injected
water also could reduce the unequal viscosity of the water and the oil
in the heated zone, and in turn, the sweep efficiency could be improved.
In this work, we injected smart water because of its
results in increasing oil recovery according to many labs works and
pilot based on the mechanisms that propose and qualify the effectiveness
of smart water flooding such as: multicomponent ion exchange[1],
double-layer expansion [2], reduction in interfacial tension and
increased pH [3],fines mobilization [4],
mineral dissolution [5], organic material desorption from the clay
surface [6], Cation exchange on quartz surface [7], desorption of
organic materials from quartz surface [8].
In the case of using thermal EOR techniques, the heat
provided to the reservoir could absolutely reduce the oil viscosity and
increase oil recovery. The economic overview, on the other hand, the
least expensive thermally technique is hot water flooding based on oil
recovery [9-11]. In this work, a combined chemical and thermal
technology was applied on Bartlesville Sandstone cores to find a
feasible, cost-effective EOR solution to increase oil recovery from
heavy oil reservoirs without using high energy methods such as thermal
techniques.
Experimental Section
Porous Media
Core samples were taken from the Bartlesville
Sandstone reservoir located in east Kansas. The cores description is
listed in Table 1.

Brines and Crude Oil
Reagent-grade salts were prepared with deionized water to
make FW and smart water. The compositions of brines are listed
in Table 2. A reservoir crude oil was delivered by Colt Energy
from Bartlesville Sandstone reservoir. The oil viscosity is ~600
cp and density 0.83 at 20°C.
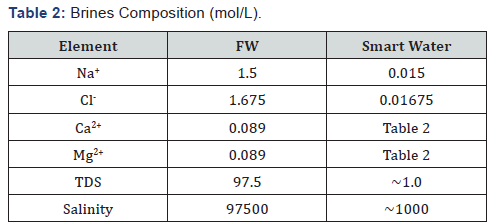
Core Preparation and Flooding
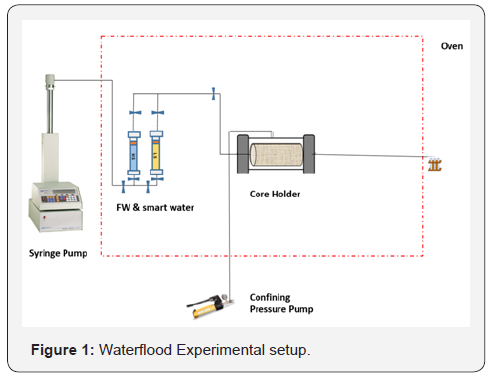
The experimental setup is shown in Figure 1. The cores
first cleaned with toluene. The cores were then evacuated and
saturated under vacuum in the FW. The same FW was used to
measure the permeability. The cores were pre-aged in heavy
crude oil for three weeks at 90°C. The water flooding was
conducted at reservoir temperature 90°C. FW was injected into
the cores until residual oil saturation was reached. After that,
smart water was injected until no more oil was produced and
injection pressure stabilized. The cores were saturated with the
same FW and smart water was injected as follows:
i. RC1: The smart water contains 45mmole of Ca2+, and
the experiment temperature was 25°C.
ii. RC2: The smart water contains 90mmole of Ca2+, and
the experiment temperature was 85°C.
iii. RC3: The smart water contains 45mmole of Mg2+, and
the experiment temperature was 25°C.
iv. RC4: The smart water contains 90mmole of Mg2+, and
the experiment temperature was 85°C.
Results and Discussion
Reservoir core (RC1) and RC2 were flooded with smart water
containing 45 and 90mmole Mg2+ at 25°C and 85°C, respectively
as described in Table 2, while both RC3 and RC4 were flooded
with smart water containing 45 and 90mmole Ca2+ at 25°C and
85°C, respectively.
RC1
The temperature of this experiment was set on 25°C. The core
successively flooded with FW and smart water. The volume of the
produced oil was collected and logged at the room temperature.
The pressure readings were also recorded. The ultimate oil
recovery was 54% of original oil in place (OOIP) after the core
flooded with FW (Figure 2). The injection pressure started with
50 psi and rose up to 180psi and dropped until stabilizingat
41psi after injecting 2PV of FW (Figure 3). The incremental
oil recovery after switching the injected brine to smart water
was 5% of OOIP. The injection pressure rose up to 64psi and
stabilized at 49psi.
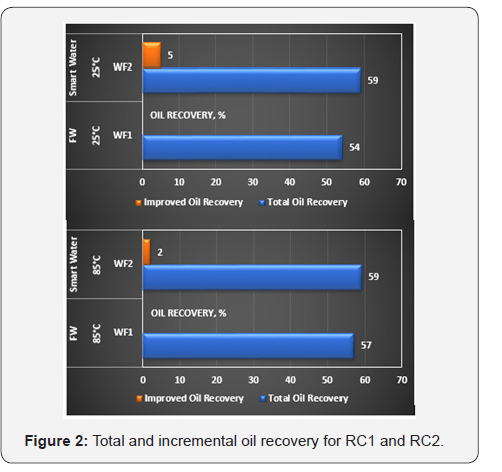
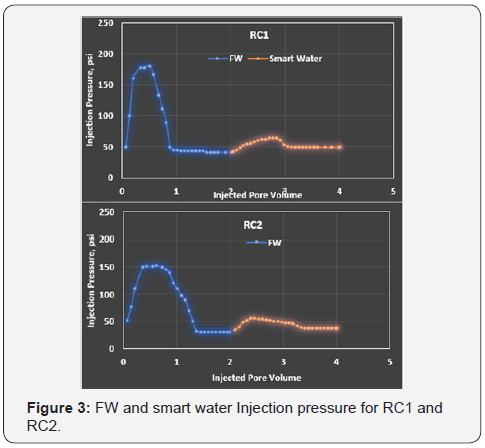
RC2
This core was flooded the same way as RC1 except the smart
water containing 90mmole of Mg2+. The temperature was
85°C for both FW and smart water flooding. The oil recovery
during secondary water flooding with FW was 57% (Figure 2),
the flooding was stopped after injecting 2PV of FW. The water
injection stopped until no more oil was produced and until
the pressure stabilized. During the FW flooding, the pressure
started 52psi. The pressure increased quickly until reaching the
maximum reading at 151psi. After the crude oil began to flow out
the core, the pressure decreased slowly until stabilizing at 31psi.
Upon switching to smart water, the incremental oil recovery was
2% of OOIP. The injection pressure increased dramatically until
reaching the highest point which was 51psi and stabilized at that
point.
RC3
This core and the following one (RC4) were flooded with
smart water containing 45 and 90mmole of Ca2+ at 25 and 85°C,
respectively. The experiment temperature is 25°C for RC3. The
oil recovery with FW was 51% of OOIP (Figure 4). The injection
pressure started with 66 psi and rose up to 160psi and then
stabilized at 52psi (Figure 5). Upon switching to smart water, the
improved oil recovery was 9% of OOIP. The injection pressure
stabilized at 59psi.
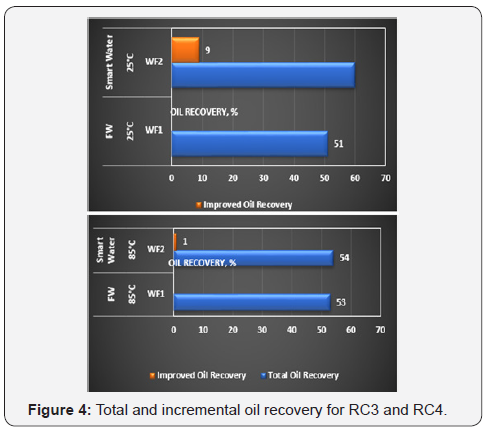
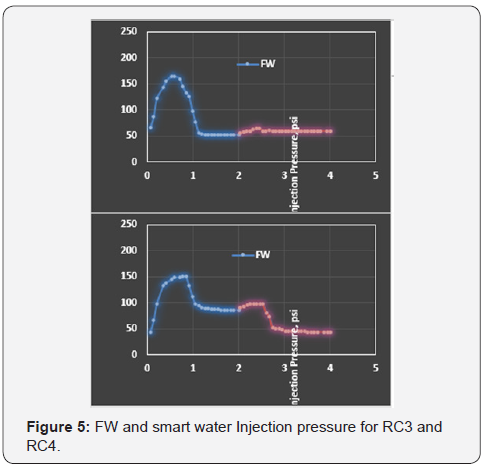
RC4
The experiment temperature was set at 85°C. The same
procedure was followed as in previous cores. After injecting
2PV of FW the oil recovery was 53% of OOIP. The recovery was
improved to 54% after the injected brine switched to smart
water, resulting in a 1% incremental recovery of OOIP. The
injection pressure stabilized at 43psi.
All Cores were similar in FW but different in the experiment
temperatures and the injected smart water. Both RC1 and RC2
were flooded using 45 and 90mmole of Mg2+ in the smart water
but at 25°C and 85°C.
Increasing concentration of Mg2+ in smart water has the
effect on reducing oil recovery during smart water flooding.
Comparing RC1 and RC2, the oil recovery from RC1 by FW was
54% of OOIP, while it was 57% of OOIP from RC2. The ultimate
oil recovery in RC2 was higher than in RC1 because the higher
temperature.
The incremental oil recovery from RC1 using smart water
was 5% of OOIP, while it was 2% of OOIP from RC2; i.e. the
improved oil recovery decreased by a factor of 2.5 when doubling
the concentration of the Mg2+ in the injected smart water even
though the temperature was higher for RC2. Similarly, comparing
RC3 with RC4, the oil recovery was 51% of OOIP for RC3 with FW
flooding, while it was 53% for RC4 also due to extra heat.
The incremental oil recovery using smart water flooding
was 9% of OOIP for RC3, while it was only 1% of OOIP for
RC4; i.e. the improved oil recovery increased by a factor of 9 if
we reduced the concentration of the Ca2+ in the injected smart
water although the temperature was ambient temperature.
Increasing the divalent cations in the injected smart water led
to decrease the adsorption of the organic material, and in turn,
the rock became too water-wet for observing smart water effect.
During FW flooding, comparing all the cores in this work, the
higher the temperature, the higher the oil recovery. Using hot
water improves the mobility ratio due to reducing the oil phase
viscosity compared with cold water. Thermal expansion of water
plays an important role in injecting hot water, the lower density
of hot water reduces thermal loses to the aquifer and speeds up
the propagation of the temperature front through the reservoir.
The effect of increasing the temperature to 85°C with a
double Mg2+ concentration in smart water (RC2) is the same as
applying 25°C with a smart water containing a half concentration
of Mg2+ (RC1). Increasing temperature to 85°C when smart water
has double Ca2+ concentration (RC4) is a wrose scenario than
using 25°C with an smart water contains a half concentration
of Ca2+ (RC3). The fuel consumption using high temperature
could be replaced chemically by controlling the divalent cations
concentration. The fuel consumption could be more feasible
when controlling the water chemistry. The good example for that
is RC3 when lowering the Ca2+ to the half and also (RC1) when
lowering the Mg2+ to the half. Applying ambient temperature
with reducing Ca2+concentration to a half provided a higher oil
recovery among all the other scenarios (60% of OOIP). Table 3
shows the summary of the results.
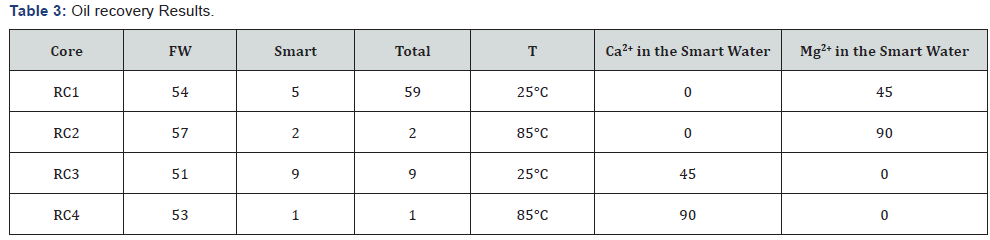
Conclusion
Increasing the temperature of the injected water reduces the
viscosity contrast between oil and water in the heated region.
This can improve the sweep efficiency. Heating the oil using
hot water could reduce the oil viscosity and in turn increase oil
recovery.
Hot water flooding may also increase the economic life of
individual wells by as much as a factor of two. Controlling the
chemistry of water could provide a better solution for increased
heavy oil recovery instead of increasing the injected water
temperature, that could lower the energy required to move the
heavy oil from the heavy oil reservoirs in general and in this
work for the eastern Kansas oil reservoirs. The conclusions can
be drawn as follows:
i. The adsorption of the organic material in heavy crude
oil on the sandstone decreased because of the rock became
too water-wet for observing smart water flooding effect when
the divalent cations presented in a higher concentration.
ii. Heating could reduce the oil viscosity, interfacial
tension, and residual oil saturation which leads to potentially
higher recovery factor. Yet, controlling the chemistry of water
(especially divalent cations) could improve oil recovery
instead of increasing the injected water temperature.
Increasing temperature with tune water concentration
providing a greater heavy crude oil recovery.
Acknowledgement
The authors would like to express their grateful acknowledge
to Colt Energy Company. The authors thank the Higher Committee
for Education Development in Iraq and the Iraqi Ministry of Oil/
Missan Oil Company for their permission to present this paper.
The authors would like to express their grateful acknowledge
for Sandia National Laboratories is a multimission laboratory
managed and operated by National Technology and Engineering
Solutions of Sandia, LLC., a wholly owned subsidiary of
Honeywell International, Inc., for the U.S. Department of Energy’s
National Nuclear Security Administration under contract DE-NA-
0003525
For more articles in Open Access Journal of
Engineering Technology please click on:
Comments
Post a Comment