Juniper publishers Production of Bisphenol A (BPA) By Green Technology
Juniper Publishers - Open Access Journal of Engineering
Technology
Authored by : Ibrahim Altuwair
Abstract
The literatures and researches show that the reaction
between phenol and acetone is too slow in the absence of catalyst, but
it proceeds with formation of Bisphenol A (BPA) in the presence of
acidic catalyst or any strong acid [1].
Although the BPA formation depends on the molar ratio of reactants
(acetone and phenol), using a different solvents or catalysts will not
deny the effect of the BPA on human health. It is only enhancing the
reaction ratio between phenol and acetone and improves the selectivity.
There are different catalysts and solvents have been tested and their
effects on the process and BPA yields were evaluated. However, as the
reaction proceeded to increase the water concentration, the inhibition
effect of water reduces the reaction rate and gives low yield. This will
not eliminate the impacts of BPA directly or indirectly on human
health, it is only increased the quality of the product.
Keywords: Bisphenol A; Process; Reaction; Acetone; Catalyst; Concentration
Abbreviations: DCM: Dichloromethane; DOE: Design Of Experiment; PTSA : P Toluene Sulfonic Acid; DVB: Divinyl Benzene; SCF: Supercritical
Introduction
Bisphenol A production process
The aim of the chapter is to give an overview of the BPA production methods.
Preparation of Bisphenol A
The BPA synthesis including mechanisms, possible reactions, by-products, and order of reaction.
The acid catalyzed condensation of acetone with two moles
of phenol is the first process for forming BPA, (Figure 1).
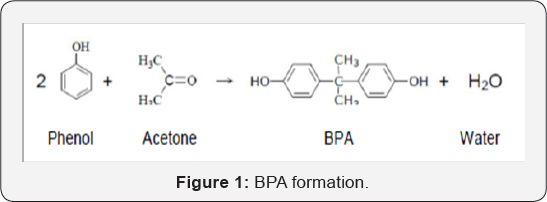
The heat of reaction, for reagents and products in
their natural physical state at 25 °C, is calculated from heats of
formation as 19kcal/mol and a molar ration of 1:2 acetone to phenol, is
considered in the first stage of the research, in the presence of
concentrated hydrochloric acid at room temperature. There was a claim of
the present of small amount of water (10%) or less in the reaction
mixture increases the reaction rate of the mixture catalyzed by
hydrochloric acid [2].
Others suggest that processing the reaction by ion-exchange resin
(sulfonic acid) modified with alkyl-SH groups enhance the reaction and
decrease the amount of water 5% by weight in the mixture which decreases
the yield
of BPA. However, it was suggested by Jerabek et al. that to reduce the
effect of water, dehydration by various water-binding agents (such as
Calcium Chloride or phenyl acetate) or by azeotropic distillation can be
used.
This reaction proceeds with an electrophilic attack
of the proton from the acidic catalyst on the molecule of acetone.
During this step, producing by-products or “impurities” might change the
mechanism of the reaction by produce undesirable products as a result
of acetone - acetone reaction or Dimerization. Thus, Mesityl oxide is
formed and increasing the number of impurities that lead to further
phenolic reaction and the process becomes more complicated. Therefore
more effects on human health are expected due to phenolic impacts.
The most industrially used processes for making BPA
in the United States and Western Europe are the acetone-phenol Process,
There are different methods of producing Bisphenol A.
Conventional Methods
This method based on the type of the catalyst and
solvent. It is also called Hydrogen Chloride-catalyzed process. The
first production of BPA was made by Russian scientist, Dianin, in 1891.
He used Hydrochloric acid to accelerate the reaction since it is hard to
form BPA without strong acid. However, the process of obtaining BPA is
also depending on the phenol to ketone (acetone) reaction ratio. Thus,
there will be excessive phenol, approximately a ratio of (3-30):1 to
ensure the reaction is processed (WO 2005/030687, 2005). Although the
reaction gives high efficiency, the conventional methods of BPA
production does not provide approximately high selectivity of the
reaction of phenol with acetone and the required purity of the desired
product. It also appeared that it is impossible to achieve the
equilibrium state for some by-product of the process therefore the
process cannot be performed for long time without production loss. In
addition, because of the low concentration of BPA, high energy
consumption will be resulting from the process.
Alternative Methods
There are alternative methods to produce BPA by using
different catalysts with/without promoters. This method is also known
as the resin-catalyzed process. It gives better results in terms of
selectivity, and purity of product. One of the catalyst that been used
such as exchanger resin also improves the production of BPA. In
addition, there are other catalysts have been used and modified to
increase the BPA concentration and improve the phenol and acetone
reaction, for instance, sulfonated ion exchange resin, DVB divinyl
benzene, and polystyrene. Although the formation of BPA is improving
continuously, still there is no answer for the variation in ratio of
phenol to acetone.
Parameters
The selection of parameters depends on the specific
compound. There are several important parameters need to be taking into
account during the process:
1) Temperature
2) Time
3) Catalyst
According to Arrhenius equation, the results obtained
were temperature dependence, for the water adsorption coefficient KW.
For the adsorption coefficient of acetone and phenol increased with the
temperature, although, the rate constant of reaction is increased with
temperature, the energy of between acetone and phenol is weaker (Figure 2).
K = 1470 Exp (-59900/RT) [m3kg-1s-1]

This showed that higher energy is needed to complete the formation of BPA due to the slow processing mixture.
Experimental Section
Experimental Procedures
P-Toluene sulfonic acid, acetone, and phenol were
purchased from Sigma-Aldrich Company. An appropriate amount of an
aqueous solution of chloroform was added to the solution at room
temperature. Synthesis of bisphenol A(BPA) was carried out in the liquid
phase under atmospheric pressure and 600C in 1000ml two-neck round
bottom flask equipped with a condenser and a magnetic stirrer. An 8.6g
of PTSA catalyst put into the reactor with 23.5g of phenol. Then, 2.9g
of acetone was added by a micro- syringe to start the bisphenol a
synthesis. Yield was determined by a column chromatography. Furthermore,
vacuuming the sample was applied after separation process to purify the
final product from the residual solvents. Weights were measured before
and after evaporation.
Characterization: Bisphenol A monomer
synthesis from the condensation reaction of phenol with acetone will be
analyzed by using Column Chromatography, NMR, GC-MS techniques.
Spectroscopic analysis showed that BPA monomer was present in the
product although significant amounts of compound formed during the
reaction and residual starting material were still present.
After sampling and cooling down the samples at 0 °C,
evaporation was applied by using rotary evaporator for 10-20 minutes at
40-60 °C . HNMR spectrum at 400MHZ was measured by a Bruker DMX500 with
the following condition; Spinning rate 5KHZ, Constant time 1.75msec,
interval 4sec, accumulation 500 times, and glycine as an external
standard of chemical shift. Before the measurement, the sample was
cooled at
-20 °C .
Materials and equipments: Phenol and acetone
as the main reactants of reaction brought from Sigma-Aldrich Company
P-toluene sulfonic acid-PTSA is available in the chemistry lab with
chloroform, Methanol, Dichloromethane DCM, acetonenitrile, (CDCl3, DMSO were used as deuterated solvents for NMR) Silica gel and Sand were also available in the lab.
250 & 1000ml two neck round bottom flask were
used, rotary evaporator R-114, water bath B-480&B-490RE Buchi,
condenser, thermometer.
Process Selection: Condensation of phenol with acetone in the presence of p-Toluene sulfonic acid (PTSA) as a catalyst.
Process Description: Acetone and excess phenol
are reacted at a temperature of 600C and atmosphere pressure by
condensation in p-Toluene Sulfonic Acid catalyzed reactor system to
produce p, p-bisphenol A, water and various by-products are also formed
in the reaction process. The crude distillation or chromatography column
helps to remove water and unreacted acetone from the reactor effluent [3].
Acetone and un reacted materials will be sent to rotary evaporation
process at 50-60 °C for more purification then mother liquor from
purification system is cooled down at -20.
Equipments Used:
1) Reactor
2) Oil bath
3) Condenser
4) Heater
5) Chromatography Column (CC)
6) Rotary Evaporator
Description
A. Components of a control System
The system is divided into the following components:
1) Process
2) Measuring element
3) Controller
B. Controlling System Used:
1) Temperature Control
2) Stirring control
3) Pressure Control
Temperature Control: It is desired to maintain
the temperature in the reactor by using a controller. If the measured
temperature differs from the desired temperature, the controller senses
the changes and modify at the required temperature.
Stirrer control: Stirring can be control by
using magnetic stirrer .In this experiment, IEC Magnetic stirrer was
used with CAT No.: CH2090-001 STIR Input: 220/240V.AC.50/60Hz.4AMP.
Pressure control: The pressure maintains at the atmospheric pressure. However, low pressure was used for some processes [4,5].
Preparation Method: The experiment carried out
in the chemistry lab based on the reaction of phenol- acetone reaction
and also the reaction will be tested in different ways. Firstly, the
reaction of acetone and phenol will be carried out. Secondly, the
homogeneous catalyst will be added. Thirdly, the reaction will be
processed in the presence of supercritical carbon dioxide, scCO2. The report will cover the first and second parts.
The main goal of the project is to use supercritical
carbon dioxide as a reaction medium for the production of BPA and also
for separation purposes to remove undesired products easily Minimizing
the effect of the undesired products on the BPA formation by using SCF
will be another target for the study as an advantage of using green
technology for BPA production and reduce the chemicals that emitted into
the atmosphere and polluted the environment. This technique will be
applied after synthesizing BPA by different methods to investigate and
evaluate their results with/without using ScCO2 technology.
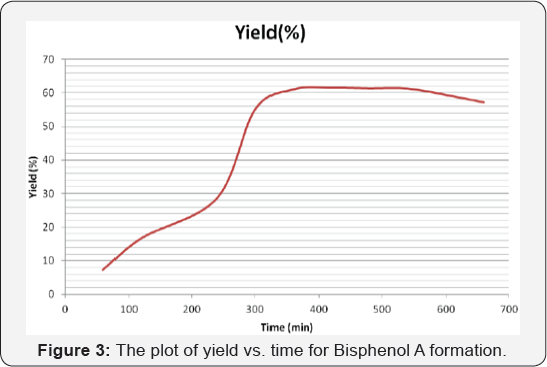
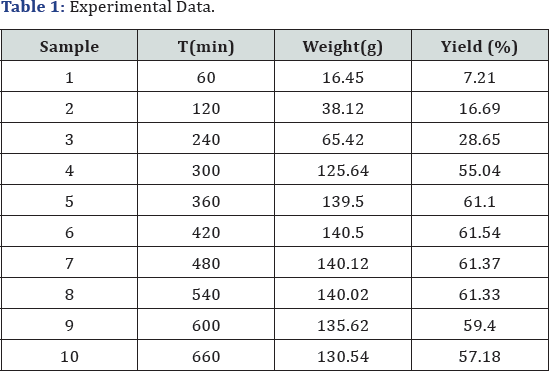
Experimental results and discussion: In order
to understand the reaction mechanism, several experiments were conducted
in the chemistry lab. These experiments were carried out at 60-800C for
all over variables, such as concentration of catalyst and reactants
fixed at maximum yield level. At the end of the experiment, the reaction
mixture was cooled down at room temperature and then stored at 20 after
dried and weighed. The
yield of the reaction mixture was calculated for each experiment. The
plot of yield vs. time is shown in Figure 3.
X = 1 - (1 + 0/03t )-2/0
Where, X: is fraction conversion of limiting component (mol/ mol) (Table 1).
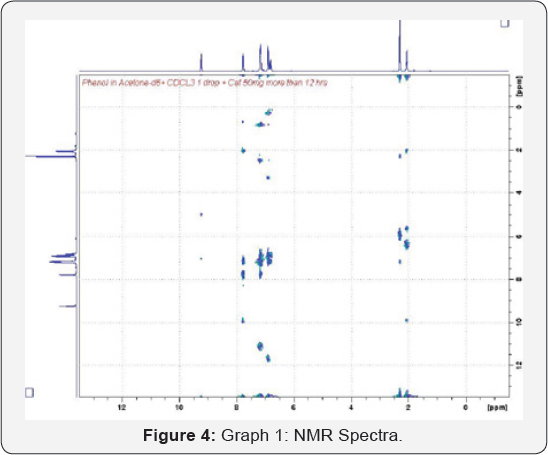
The graph is in a good agreement with literature data, this plot was generated based on experimental data (Figure 4) (Table 2).
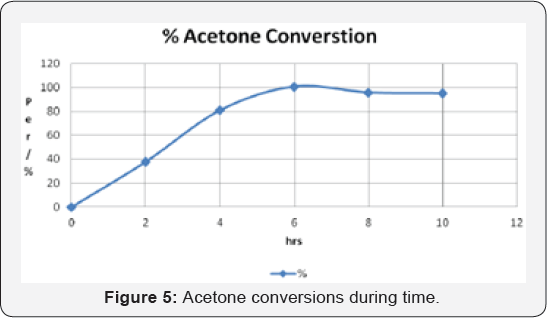
Conversion %= R/(1+2R)
R: Ratio
Ratio= F / G
G: (A + B ) / 5
F: (C + D ) / 8
(Figure 5)
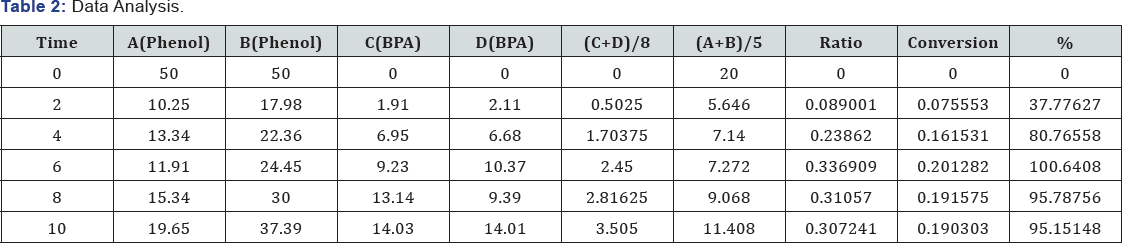
Analysis
The samples were analyzed by HNMR (Gyro and Flip
Machines). Gyro system was used to analyze the structure of the product
where flip was used for kinetic reaction purpose. All procedures and
results of the analysis are described in the following sections. The
graph shows the total acetone converted to product and time needed for
completion. It is very clear that after 6 hours of reaction, the whole
acetone converted to products.
Design of Experiment (DOE)
The following section will be focus on the
experimental design to investigate and evaluate the individual and
interaction effect. Using different techniques to deal with noise in an
experiment, and make a good decision for the chemical process. To design
an experiment by using engineering method or program, the following
steps need to be investigated:
1) Response Variables
2) Factors
3) Randomization
4) Repetition and Replication
Response Variables: Response Variables are the
variables that measured and the object of the characterization or
optimization (Y's). However, defining the response will be the hardest
part to design an experiment. To solve this problem, several questions
have to be answer such as:
a. How will the results be analyzed
b. How good is the measurement system?
c. What are the baseline mean and standard deviation?
Factors: They are variables which controlled
or varied in a systematic way during the experiment. These two steps are
important to design the experiment and evaluate or investigate the
factors effect on the process.
The purpose of using an experimental design is to
deal with different factors and make a good decision for an optimal
production process. Before starting the design of experiment DOE,
pre-experimental plan is recommended.
a. Experimental Design Procedures
Planning: Before starting the computer
program, pre- experimental planning needs to be done. t\The preparation
require before beginning experimentation depends on your problem. For
example, you need to determine what influence factors are, what
processing condition influence, thus careful planning can help to avoid
problem that can occur during the execution of the experimental plan.
Processing Characterization (Screening): In
many process development and manufacturing applications, potentially
influential variables are numerous. Screening reduces the number of
variables by identifying the key variables that affect product quality.
This reduction allows focusing on the really important variables.
Screening may also suggest the best or optimal setting for these
factors. Then you can use optimization methods to determine the best
settings and define the nature of the curvature. Screening test by
running a relatively small number of tests to isolate the most important
factors.
Optimization: (optimize a process/product):
The method of optimization helps to determine the best settings and
define the nature of the curvature. The optimal values for experimental
factors depend on the process objectives. The objective of this
experimental is to reduce by-products and maximize the BPA Yield.
Randomization: It can be done in many ways
a. Run the treatment combination in random order
b. Assign experimental units to the treatment combinations randomly
c. The advantage of randomization is to average out
the effect of the extraneous factors (called noise) that may be present
but were not controlled or measured during the experiment.
d. Spread the effects of the noise across all runs
e. These extraneous factors (noise) cause unexplained variation in the response variable (Yield).
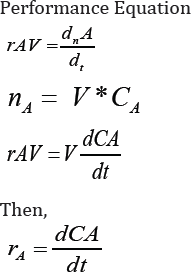
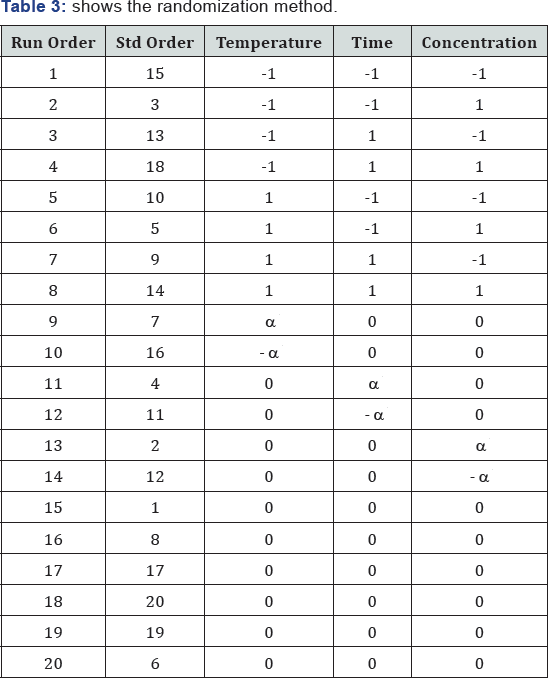

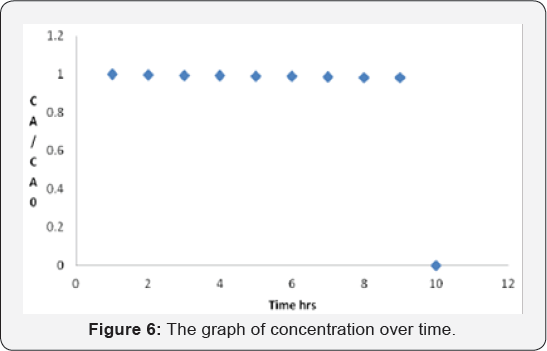
Minitab Program
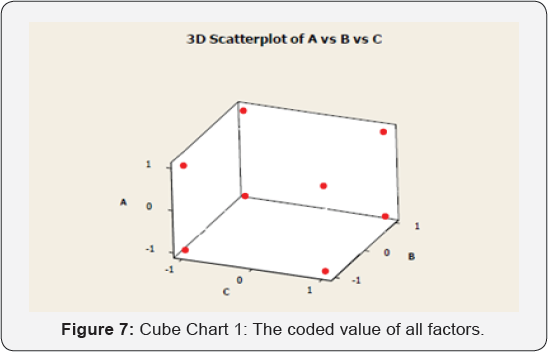
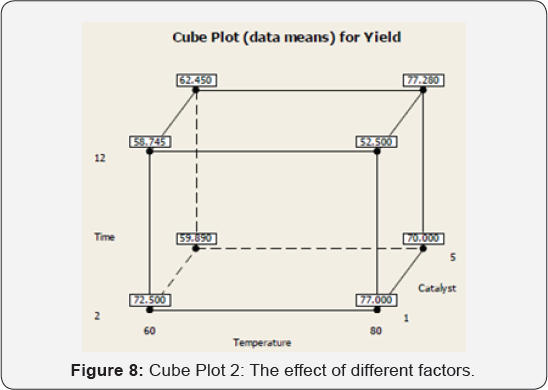
The below cube chart shows the coded value of all factors from high to low values (1to-1) (Figure 7,8).
The Cube Chart, the effect of different factors can be calculated by applying the following equation:
Effect = [(+Y / n ) - (-Y / n )]
Interaction plot
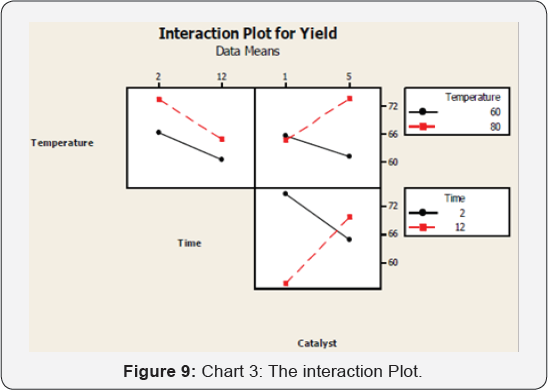
The following graphs show the interaction effect of
the different parameters on the process. The interaction between
catalyst and time has the greatest or significant effect on the process
followed by the interaction effect of catalyst and temperature then time
and temperature interaction effect.
By using the Minitab Programm, it is easy to evaluate
the significant factors with significant effects on the reaction
process and eliminate all factors without real effect on the process.
Also the program minimize the time that will be spent during the
reaction and focus only on the significant factors which will save time
and money (Figure 9).
Results and Discussion
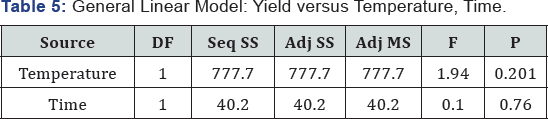
General linear model: Yield versus temperature, time (Table 5)
Factorial fit: Yield versus temperature, time, catalyst (Table
6) : Estimated Effects and Coefficients for Yield (coded units)
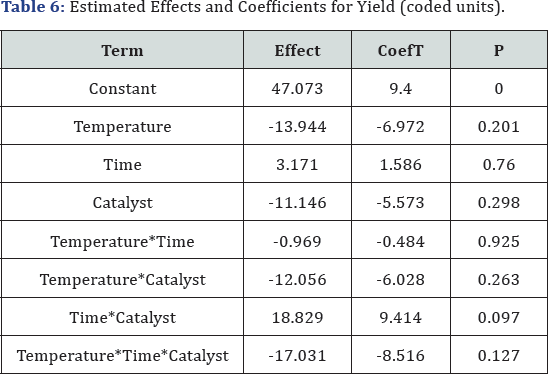
Al these values demonstrate the interaction effects
on the process such as Temperature and catalyst interaction that have
significant affects by high effect value and lowest P-value.
Evaluation
The mechanism of bisphenol reaction from industrial
starting material was studied. The obtained yield -time relationship was
obtained .It was found that at about 62% can be obtained after 6 hours
of reaction.
The experimental design detects the effects of
different factors on the process. In addition, the experimental data
shows the reaction rate of the starting materials and final products
which is in agreement with the HNMR spectra results even though there
were some experimental errors due to the equipments and measurement
errors. In addition, designing the experiment by DOE presents the
experiment by engineering way and save time and money for future
research.
Drawbacks
Bisphenol A-BPA production process is continuously
improved by different ways even by manipulating parameters. However,
there's no answer to stoichiometric ration acetone to phenol variation
from 1-2 to 1-10 or 30, which add extra processing required during
purification. Thus, the reaction becomes more complicated (Figure 10).
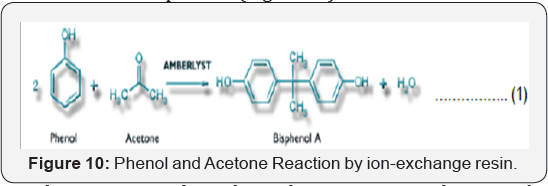
The reaction is the industrial reaction to produce
BPA by using ion exchange resin. The Reaction shows that swollen ion
exchange resin with SO3H group attacks the aromatic ring to form BPA. Firstly, SO3H
group will react with carbonyl group (acetone) by less than completing
proton H+ and then acetone will react with phenol to give the final
product of BPA, the two aromatic rings shown on the BPA structure
describe the need of excessive phenol to react with one acetone in order
to produce BPA and water. However, producing water decreases the
catalytic activity of the resin. As water spreads towards the outlet,
the acetone conversion decreases [6].
This accumulation of water prevents a long-term
operation of the process; therefore, to stabilize the operation process,
water must be removed. Producing water during the reaction, slow down
the reaction and decrease the concentration of the product.
Basics of Supercritical Fluids
Supercritical fluid (SCF)
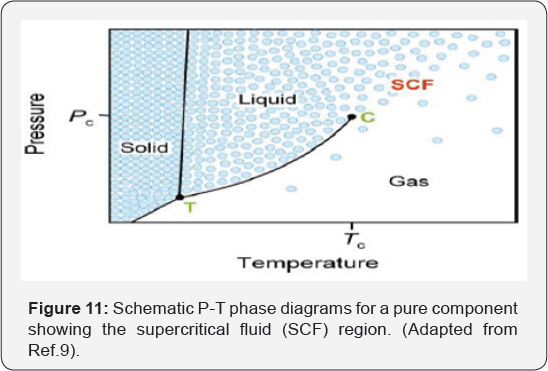
The triple point (T) and critical point (C) are
marked. The blue circle represents the variation in density of the
substance in the different regions of the phase diagram. Note that the
density varies continuously between the liquid state and the gas state,
providing the liquid-gas equilibrium (Figure 11).
Three different phases of the compound-solid, liquid
and gas are also shown. With an increase in temperature and pressure,
there comes a point when the compound shows intermediate properties
between those of a pure liquid and a pure gas that is the critical
point. The region beyond that critical point is the supercritical fluid.
Definition
What is supercritical fluids?: When the
temperature and pressure of a one-component fluid exceed its critical
temperature and pressure, it is said to be supercritical fluids. It is
neither liquid, nor gas as shown in the diagram and that give no any
clue to predict the properties of supercritical fluids (SCF). Therefore,
supercritical fluids are influencing the chemical processes in many
ways. They can be used as solvents since they have unique properties to
become as liquids and as gases together Furthermore, these properties
offer distinct advantages such as:
Gas-Expanded liquids (GXLs)
A Gas-expanded liquid (GXL) is mixed solvent composed
of a compressible gas such as carbon dioxide or ethane dissolved in an
organic solvent. In other words, it is the ability of the gas to expand
the liquid (solvent) and improve the physical and chemical properties of
the liquid (Figure 3b).
It is considered a magical chemical due to their unique properties. As
Jessop's group mentioned, (GXLs) are the promising alternative media for
performing synthesis, and separation [7] (Figure 12).
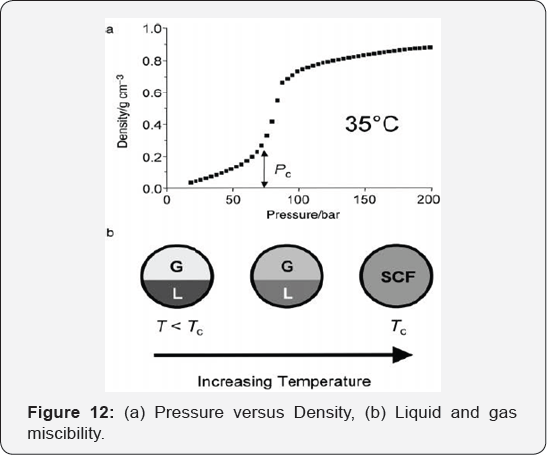
Figure 12a Graph showing the variation in density for pure CO2 at 35 °C. At this temperature (i.e., close to Tc for CO2)
there is a rapid but continuous increase in density near the critical
pressure (Pc). (b) Schematic representation of the change from
liquid+gas equilibrium (T
Supercritical carbon dioxide (SCCO2)
Supercritical carbon dioxide (SCCO2),at (Tc=304.1K, Pc=7.38MPa),
is the promising green solvent due to it is unique
property and behavior such as non-flammable, inexpensive, and
environmentally friendly and safe. It is also available abundantly. Many
researchers have shown that carbon dioxide has a high potential as a
solvent for many organic compounds and widely used for practical
application [8] (Figure 13).
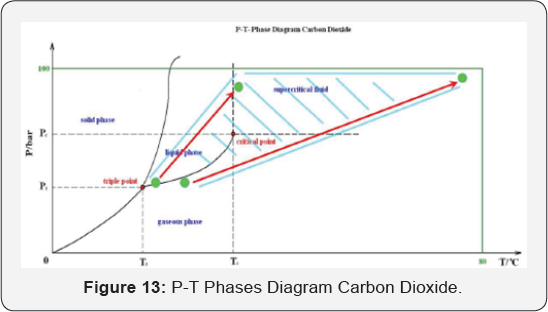
This diagram shows the P-T phase diagram with the region of supercritical Carbon dioxide properties (Tc=304.1K, Pc=7.38MPa).
Applications of supercritical carbon dioxide: The
application of supercritical carbon dioxide (scCO2) as a
solvent has been on the rise. This is because of its low toxicity and
its usage in compound extraction. Further, it has a higher stability for
the different process reactions and need low temperatures for any
process to compare with other solvents [9]. Perhaps the most common use of supercritical carbon dioxide scCO2
is in the coffee industry. In addition, the application of
supercritical carbon dioxide has found its way into the pharmaceutical
industry. It is used in the production of micro-and nano-scale particles
[1].
Polymerization is another area that makes use of supercritical carbon
dioxide. It has proved to be a good nonpolar solvent for organic
compounds such as alkanes, alkenes, aromatics, and alcohols which can
easily dissolve in supercritical carbon dioxide. It is seen that polar
molecules such as sugars and other inorganic salts are insoluble but by
increasing the pressure of supercritical fluid, the dissolving power can
be improved [8].
Many studies noted that advantages of supercritical carbon dioxide are
attracting industries due to that they are inexpensive, non-toxic, can
be recycled, and has easily accessible critical conditions. Also,
supercritical carbon dioxide scCO2 processing of polymer uses
the liquid-like densities and gas-like mass transfer properties of
dense gases (DGs) to provide more controlled and more efficient methods
of polymers preparation. Also provides an environmentally benign method
for creating polymer compared with conventional processing that increase
the environmental threat by emitting Volatile Organic Compounds VOC's
and other polluted compounds into the atmosphere.
Supercritical fluids applications:
a. Supercritical Extraction
b. Particle formation
1. Particles from Gas-Saturated Solution (PGSS)
2. Gas Anti solvent (GAS)
3. Precipitation with Compressed Ant solvent (PCA)
4. Solution-Enhanced Dispersion by Supercritical Fluids (SEDS)
5. Depressurization of an Expanded Liquid Organic Solution (DELOS).
c. Supercritical Fluid Chromatography
d. Separations and crystallization
Synthesis and processing: The review focuses on recent advance in polymer synthesis and processing using liquid and supercritical carbon dioxide scCO2.
The synthetic techniques discussed include homogeneous solution
polymerization and heterogeneous and the variable solvents strength
associated with supercritical fluids have been used in areas such as
polymer fractionation and polymer extraction. Furthermore, the unique
physical properties associated with supercritical fluids give rise to a
range of possibilities for the chemical materials. Not only in polymer
science but also in organic synthesis, heterogeneous and homogeneous
catalysts. In the case supercritical carbon dioxide (SCCO2), there are chemical, environmental, and economic benefits that will be captured from its use as a solvent.
In addition, supercritical carbon dioxide technology has several advantages over conventional solvents as a reaction media [3].
The unique property of supercritical fluids observed from different SCF
experiments maybe used to manipulate chemical reactions to make them
more efficient or specific. In addition, SCF has a great miscibility
which might change heterogeneous reactions and become homogenous
reactions and the yield can be greatly improved [3]. Furthermore, it is stated that using scCO2 as a reaction media will change the properties of the reaction and enhance the reaction rate as well as the yield.
Separation
Beside the well-known environmental aspects of supercritical carbon dioxide (SCCO2),
it is also advantageous in the separation process as solvent due to its
preferable critical properties (Tc=304.1K, Pc=7.38 MPa) [10].
Using supercritical fluid to separate mixture compounds is an
interesting technique due to not tend to leave any toxic residuals or
cause potential thermal degradation of the product [10].
On the other hand, conventional solvents where used for separation
purpose are environmentally dangerous and create chemical waste that
supporting the phenomenon of greenhouse gases such as volatile organic
solvents (VOC).
Extraction
Extraction by Supercritical Fluids gives clean and
efficient technique compared to other techniques .Extraction by
supercritical fluids (SFE) technologies will enable solutes to dissolve
in the supercritical carbon dioxide (scCO2) and precipitated
by reducing the pressure of the fluid phase. The supercritical carbon
dioxide is then expanded to remove the solutes, and the gas is recycled
for repeated use [3]. Decaffeinated coffee and hop extracts are good examples for the application of extraction by using supercritical CO2.
However, BPA solubility in supercritical carbon dioxide will play an
important role in the BPA extraction process since it is barely soluble
in SCCO2 and become easy to be extracted (Figure 14).

Supercritical fluids reaction
There is no attention been given to this topic to
classify the physical and chemical states of the supercritical carbon
dioxide as a reaction media to produce Bisphenol A-BPA. The unique
properties of supercritical fluids observed from different SFE
experiments used to make the reaction more efficient has been determined
to be used as a reaction media for BPA. In addition, a study made by
Chen et. al. showed that using scCO2 as a reaction media will
enhance the reaction rate and yield even though Liu group mentioned
that BPA was insoluble in supercritical CO2. Therefore, the study will focus on the chemical reaction of supercritical carbon dioxide.
Acetone
Acetone is an organic compound. Colourless, flammable liquid, and the simplest example of ketone with formula of (CH3)2CO.
As Gates et al mentioned, the reaction of acetone with phenol is too
slow in the absence of catalyst, but in the presence of acid resin, it
proceeds with the formation of BPA. From the theoretical viewpoint,
acetone with SCCO2, solubility of acetone in SCCO2 was increased with pressure and temperature [11].
Many papers showed that the solubility of acetone in supercritical
carbon dioxide increased based on the condition of pressure and
temperature [12].
However, diffusivity of the acetone affected by temperature, as the
temperature increased the diffusion coefficient of acetone in SCCO2 increased at lower pressure [12]. Therefore, both temperature and pressure have significant effects on the diffusivity and solubility equilibrium [9]. Although acetone chemically instable, it is very obvious that acetone is soluble in SCCO2 under certain conditions which will help to get rid of the undesired products forms by AcetoneAcetone Reaction (Figure 15 & 16).

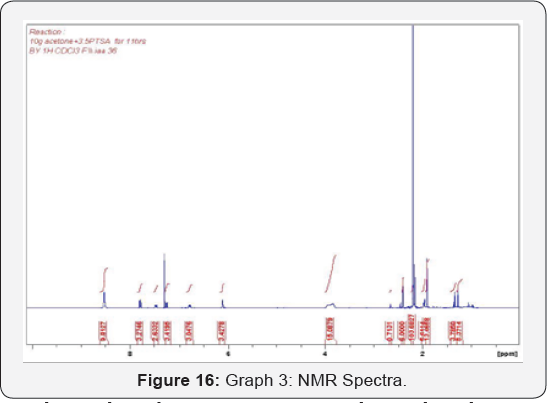
The analysis by NMR instrument shows that there are
several products made by the reaction with small percentage but the main
by-product is Mesityl Oxide which is detected by the analysis. It is an
important by-product in this reaction because of it's high reactivity
with other reactants. The study also focuses on the product as one of
the research goals.
Phenol
Phenol is a chemical compound consist of hydroxyl
group (OH) connected to an aromatic hydrocarbon group. Phenol has strong
acidity due to the aromatic ring. Its chemical formula is C6H5OH. The
chemical properties of phenol are unique due to the presence of hydroxyl
group and an aromatic ring which are complementary to each other in
facilitating both electrophilic and nucleophilic type of reaction (BPA
reaction is electrophilic) In addition, phenol has an extremely high
reactivity of its ring toward electrophilic substitution and assists its
acid catalyzed reaction with acetone leading to phenolic resin. Phenol
can be produced industrially with acetone by the cumene-to-phenol
process, there are more than 97% of phenol produced by this process
which reported by Hock and Lang. The cumene-to- phenol process was
developed on a commercial scale by Distillers
Co. in Great Britain and Hercules Powder Company in USA. The first
production plant was commenced in 1952 in Shawinigan, Canada. Today
several licensors offer their technology such as KBR or UOP. Although
all these processes use the principle of Hock synthesis, there are
differences in the design and operation of the reaction units and
distillation unit (Figure 17 & 18).
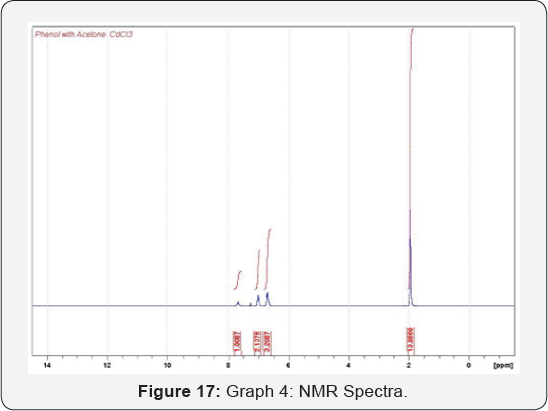
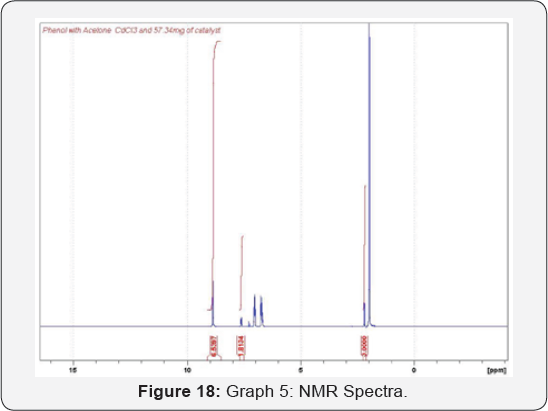
The analysis made by NMR Spectrum for Phenol and
Acetone in the presence of catalyst which gives BPA. The Spectra showed
the development of the product while the reactant disappeared.
Solubility
Solubility is a crude property used for determining
the identity of an organic compound. It can be defined as the amount of
solute that dissolves in a given amount of solvent at a definite
temperature to yield a solution that is saturated in nature. However,
solubility is affected by several factors such as pressure, temperature,
and nature of solute and solvent [13].
Many studies on solubility in supercritical fluids have grown
drastically in recent years. This due to the large range of applications
of supercritical fluids in the fields of pharmaceutical, food,
environmental, and industrial process. The fact that the properties of
supercritical fluid can be varied from gas-like to liquid-like values by
changing the pressure makes it very interesting and useful. In
addition, solubility is the most important criterion affecting the
efficacy of most of the supercritical fluid processes [13].
It has a direct impact on the rate, yield, design, and economy of the
process, depending on the process of interest, high solubility or low
solubility may be desired, for instance, high solubility is required to
manufacture particle. In the case of BPA synthesis, solubility of
reagents in supercritical carbon dioxide is important to accelerate the
rate of reaction and enhance the reaction between acetone and phenol,
thus elimination of undesired products will be achieved [13].
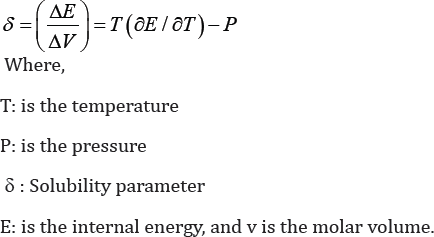
Several studies were able to observe that an increase
in temperature of certain compounds could remove the gas-liquid
boundary. In the reaction of phenol with acetone, solubility improves as
the difference between solubility parameter of the solute and solvents
decrease [14].
The effect of Temperature and pressure will change the solubility
mixture. However, the problem of selectivity of the reaction of acetone
with phenol to form BPA has not been solved and the consumption of
phenol and acetone still differs from the stoichiometric data.
Manufacturing
The most industrially used process for making BPA are
acetone-phenol process, in homogenous and heterogeneous catalysts.
Considering the costs involved and the net advantages the heterogeneous
catalysts offers, the resin-catalyzed process is preferred and it has
been improved continuously. A process which considers reacting acetone
with very little excess phenol (1:4 or 1: 10) was reported by Azam and
his group [15].
The reaction of this process consists of two steps. In the first step,
the acetone is reacted with very little excess phenol in the presence of
a resin catalyst to convert 20 - 60 % of acetone. In the second step,
the reaction mixture from the first step will be reacted in the presence
of hydrochloric acid as a catalyst. Although there were different
processes using alternative feeds, by-products still come out with the
product mixture. Thus Purification is required.
Purification
The current process used to produce BPA influences
the composition of the mixture from the reactor. It is still expected to
contain phenol, acid catalyst (unless an acid ion- exchange resin is
used), water, BPA, by-products, and some acetone. For example, a crude
product stream consisted of 40% BPA, 36.2% o, p-isomer, 1.1% o,
o-isomer, 14.2% phenol, 3.5% Chroman, 0.05% flavan and 12% of undefined
materials. However, the composition of the BPA unusually available on
the market is 95% BPA, 3% Triphenol, 1%chromanes, less than 1% o,
p-isomer, and very small percentage of others. However, the BPA
production is continuously improving by using different purification
methods or even by changing small differences in the operating condition
which may be have considerable effect on the process. Evaporation and
Colum chromatography have been used in the current experiment for more
purification [16-18].
Purification processes: Bisphenol A separation
can be done in different ways such as evaporation, crystallization,
filtration, and centrifugation. Vacuum distillation was used in this
experiment to distill out the phenol at certain conditions. More
purification was applied on the crude BPA to remove all undesired
materials by using Colum chromatography.
Based upon these initial observations, plans were
made to use dry column chromatography on the crude reaction product (tar
residue) to separate the suspected phenol product from the reaction
mixture and unequivocally identify that material as phenol using TLC,
NMR, FTIR, and GC/MS techniques.
Colum chromatography: In column
chromatography, the stationary phase, a solid adsorbent, is placed in
vertical glass usually column. The mobile phase, a liquid, is added to
the top and flows down through the column by either gravity or external
pressure. Column chromatography is generally used as a purification
technique to isolated desired compounds from a mixture [19].
The mixture to be analyzed by column chromatography
is placed inside the top of the column. The liquid solvent (the eluent)
is passed through the column by gravity or by the application of the air
pressure. Because of the different components in the mixture have
different interactions with the stationary and mobile phases, they will
be carried along with the mobile phase to varying degrees and a
separation will be achieved. The elutants or individual components are
collected as the solvent drips from the bottom of the column. There are
two categories for column chromatography separation:
a. Gravity column chromatography, when the solvent is forced down the column by gravity.
b. Flash chromatography, when the solvent is forced down the column by positive air pressure.
Procedure for dry column chromatography of crude reaction product:
A solution of tar residue (crude product) from the reaction, dry silica
gel powder (column chromatography grade-250 mesh) until all of the
solution was absorbed into the silica powder which was then air-dried to
produce a free flowing powder containing crude reaction product. This
powder was added to the top of a dry column of silica gel (1” diameter
& 20” length) in preparation for preliminary cleanup of the reaction
mixture. The column was elute with a total amount of 100 ml dichloro
form methane (DCM) and methanol (meOH), producing an initial band of
product that eluted from the column and was collected in labelled beaker
1. After the DCM elution completed, the collected amount of product
evaporated immediately on a rotary evaporator to make sure that
sufficient product was isolated for unequivocal identification of the
phenol component. An estimate of the yield from the reaction was made at
that time; however, TLC analysis indicated the presence of the phenol
component (estimated by darkness intensity of product spot). Two
solvents mixture were tested:
1) Aceto nitrile CH3CN and Dichloromethane DCM CH2Cl2
2) MeOH and Dichloroformmethane DCM CH2Cl2
Up to this time, however, the isolation of phenol
component was only suspected from TLC evidence, not proven by
unequivocal means. Analysis of the reaction products using GC-MS and LC-
MS, confirmed the presence of phenol but NMR technique was used in this
reaction to detect the structure of bisphenol A and phenol as un
reacted compound (Figure 19) [20-23].

The absorbent: The absorbent used in the experiment is silica gel (SiO2) which is solid 130-400.
The solvent: The polarity of the solvent which
is passed through the column affects the relative rates at which
compounds move through the column. Polar solvents can be more
effectively compete with polar molecules of a mixture for the polar
sites on the adsorbent surface and will also better solvate the polar
constituents. Consequently, a highly polar solvent will move even highly
polar molecules rapidly through the column. If the solvent is too
polar, movement becomes too rapid, and little or no separation of the
components of the mixture will result, but if the solvent is not polar
enough, no compounds will elute from the column. Proper choice of an
eluting solvent is essential for better separation [24-26].
Sand: It was recommended to use sand in the column to enhance separation and stabilize the stationary phase in the column.
Thin-layer chromatography (TLC): It is a
method used by organic chemistry labs and the most common method. It is
generally used to analyze and determine the system for a column
chromatography separation.
Thin-layer Chromatography (TLC) analysis is to
determine the components present within the reaction mixture. TLC
analysis (multiple elutions using Methanol/Dichloromethane) indicates
that the reaction mixture isolated from the product contained a
multitude by its Rf value in comparison to the Rf value obtained for
authentic phenol. Short-wavelength UV light was used to visualize the
otherwise colorless spots on TLC, which appeared as a dark shadows
against a green fluorescent background. Authentic phenol was spotted
alongside the reaction product showing a spot exhibiting Rf identical
with that attribute to the phenol component in the reaction mixture. TLC
obtained for crude product isolated from reaction mixture showed a
sizeable spot coinciding in Rf with the Rf value exhibited by an
authentic phenol spot. Based upon these initial observations, plans were
made to use dry column chromatography on the crude reaction product
(tar residue) to separate the suspected phenol product from the reaction
mixture and unequivocally identify that material as phenol using TL [27].
Physical properties
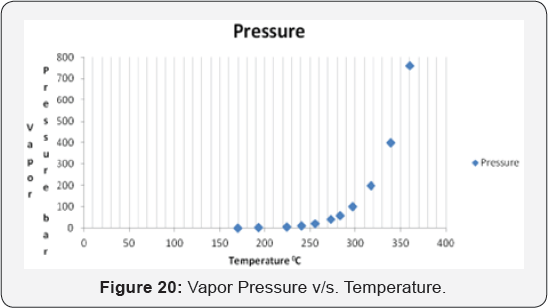
Bisphenol A is a white crystalline solid, appearing
like small white to light brown flakes or powder, with mild phenolic
odor, moderately high in water solubility (120mg/l at 25 °C). It is
specific gravity is given as 1.195 at 25 °C. It is vapor pressure is
(5.32*10'5pa m3mol-1. It is melt at 157 °C . It should be emphasized that the vapor pressure considerably increases at increasing temperature. Table 7: Bisphenol A Properties (Figure 20).
The graph shows the relationship between the vapor
pressure of BPA with temperature. The pressure will be increased with
the increasing temperature; therefore, the temperature needs to be as
low as possible. It is recommended that the preferable temperature for
process production ranged between 50-200 °C (Figure 21).
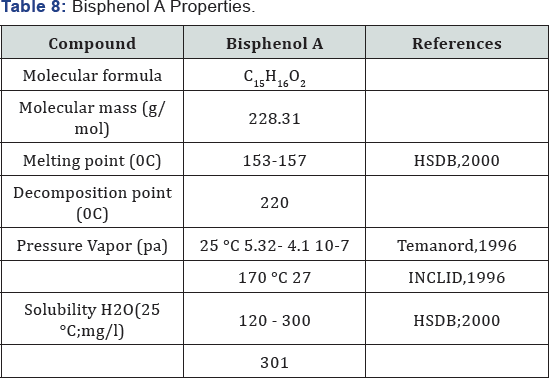
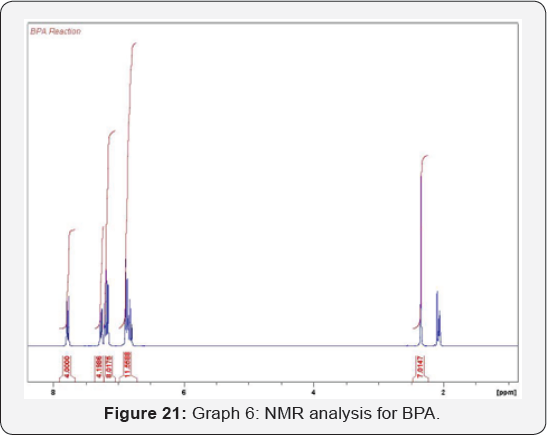
Apparatus
A liquid chromatography system consisting of binary
pump (Spectra Physics (SP), P2000 LC) with helium degassing kit was
used. The data-jet integrator was connected via Lab net to a personal
computer with SP Winner for Windows software. The fluorescence detector
was from Perkin Elmer (PE LS 40). The ultraviolet detector was from SP
(UV 2000), with scanning function on eluting peaks for the second and
third confirmation options [28]. High Pressure Liquid Chromatography (HPLC) will be used to analyze and identify the desired and undesired products.
Chromatography conditions
An injection system with a 50μL loop was used.
Fluorescence Detector. Settings: extraction wavelength, 225nm and
emission wavelength, 305nm.
Ultraviolet Detector, The wavelength was set at 225nm
(only for second confirmation option); scanning between 190 and 340nm
(third confirmation option).
Column, Length, 15nm; internal diameter, 4.6mm;
packing, 5μ Spherisorb ODS2. Elution Program for Gradient Method.
Gradient elution consisted of a 2-min isocratic elution with aceto
nitrile-water (30:70); an 18-min linear gradient to 80% aceto nitrile, a
3-min linear Gradient to 100% aceto nitrile, and a 2-min isocratic
elution at 100% aceto nitrile [29].
NMR
What is NMR?
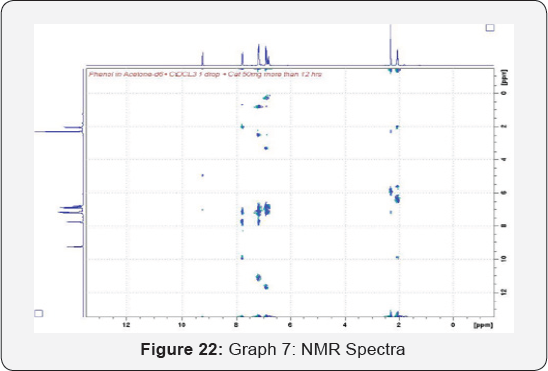
It is Nuclear magnetic resonance, or NMR as it is
abbreviated by scientists, is phenomenon which occurs when the nuclei of
certain atoms are immersed in a static magnetic field. Most of the
matter that can be examined with NMR is composed of molecules which are
composed of atoms (Figure 22 & 23) (Table 7).
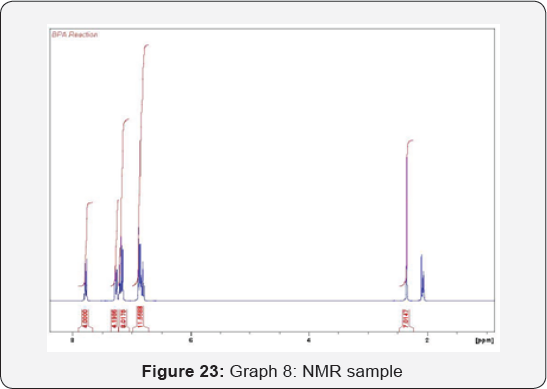
The graph presents the starting material (phenol)
disappearance through the reaction time. Phenol protons (phenol A &
Phenol B) decreased while the final product will appear slowly during
the reaction until BPA completely formed (Figure 24 & 25).
The curve shows the reaction of phenol during the reaction.
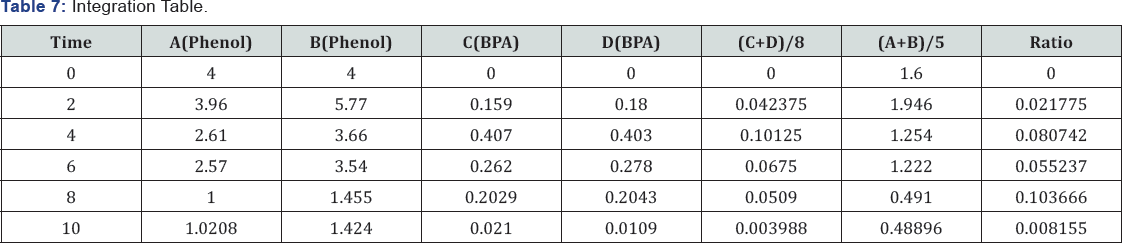
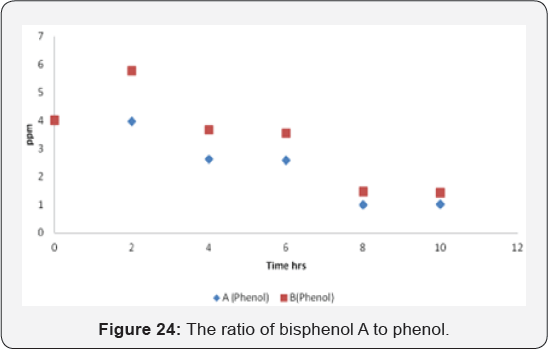
HNMR-Spectroscopy
Spectroscopy is the study ofthe interaction of
electromagnetic radiation with matter. Nuclear magnetic resonance
spectroscopy
is the use of the NMR phenomenon to study physical, chemical and
biological properties of matter. As a consequence, NMR spectroscopy
finds applications in several areas of science. NMR spectroscopy is
routinely used by chemists to study chemical structure using simple
one-dimensional techniques. Twodimensional techniques are used to
determine the structure of more complicated molecules. These techniques
are replacing X-ray crystallography for the determination of protein
structure also. Furthermore, the versatility of NMR makes it pervasive
in the sciences. This is just a basic principle necessary to begin using
NMR Spectroscopy. NMR Spectroscopy will be a useful technique to be
used to measure the amount of BPA produced [30].
The experiment will be carried out in the chemistry
lab to apply the reaction and measure all the factors, where other
techniques such as HNMR, CC, and TLC will be explained in the following
sections.
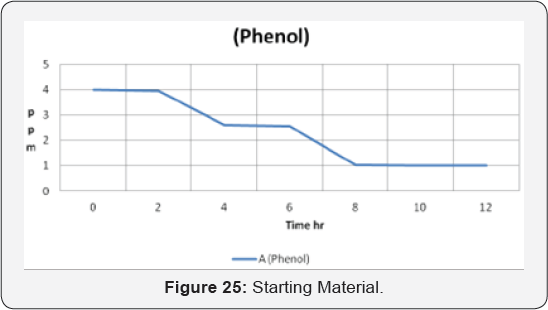
Reactor loading and set-up
1) Put on protective clothing, lab coat, goggles, and gloves. All the steps were performed in the fume hood.
2) Weigh the desired quantity of catalyst (10%) in a clean measuring dish.
3) Transfer the catalyst into the flask.
4) Weigh the desired quantities of phenol and acetone (4.7g or 23.5g of phenol and 0.58g or 2.90g of acetone).
5) Add the measured quantities of reagents to the reactor
6) Turn on cooling water to condenser
7) Turn on Magnetic stirrer
8) Turn on the heat and adjust the thermostat for the desired temperature.
NMR tube reaction
1) Weigh a clean, empty NMR tube.
2) Weigh 0.05g of catalyst in the NMR tube. To avoid transfer losses, the desired quantity was measured directly in the tube.
3) Prepare a mixture of acetone and phenol with ration of 1:2 acetone to phenol.
4) Take 40|il of the mixture with Pipette and put them into the tube.
5) Add 600|il of deuterated chloroform to the tube
6) Cover The NMR tube and seal carefully with para film.
7) Insert the tube in the appropriate spinner and adjust the depth using the sample depth gauge.
8) Turn on the air and position the tube in the magnet.
9) Lower the tube into the magnet by turning the air off.
10) Start the spinning air.
11) When the spinning rate reaches its set value, adjust lock power and lock gain.
12) Center and then lock signal.
13) Start heating the magnet by turning on the
heater, setting the temperature at 343K, and increase the air flow
through the magnet.
14) Once the temperature is reached, shim the field, and start the routine for data acquisition.
Reactor shut-down and clean up procedure
1) Put on protective clothing, lab coat, goggles, and gloves
2) Turn off the heater.
3) Turn off the magnetic stirrer.
4) Turn off the cooling water to the condenser
5) When reactor is at room temperature, remove the reactor from the C-Clamp.
6) Distill it out by Rotary evaporator
7) Take the weight of the sample
8) Put the sample in the fridge at -200C
9) Then take analyze the sample.
10) Wash flask, the stopper, and the thermometer with
acetone, then with water and soap, then with distilled water, and allow
them to dry.
11) Rinse thoroughly the sampling syringe with acetone to remove any residuals.
NMR tube reaction
1) Remove the tube from the magnet.
2) Turn off the heater, and set the temperature back to the room temperature value.
3) When the magnet cooled down, reduce the air flow through the magnet.
Summary
The review covers important aspects and present a new
way of producing a chemical/organic material, BPA, which is important
as the main feedstock for polycarbonate production. However, there are
gray areas among catalysts type that might be used during the reaction
with high efficiency. The paper presenting a solution of using
supercritical fluid as a green technology in order to produce bisphenol A
(BPA), which can be used as an essential part of polycarbonate
synthesis. To limit the use of conventional methods, new and reliable
methods have to be applied and by using supercritical fluid technology
to produce BPA as a high chemical scale production, many industrial
productions will be changed. Finally, supercritical carbon dioxide has
shown its applicability for food, pharmaceutical, medical, and chemical
processes. The work presented in this study focused on bisphenol a
processing and the purpose of this paper is to:
1) Identify new suitable catalysts for BPA formation
2) Find appropriate reaction conditions
3) Determine the reaction conditions that significantly influence the process and explain their influence.
The analysis of experimental design shows that the
interaction effect of temperature with catalyst has significant effects
on BPA yields. Furthermore, the interaction effect of temperature with
time has also a significant effect on the process but in the present of a
strong catalyst with the optimal operating conditions for maximum
yield. Whilst individual effects of time and concentration have minor
impacts on the process.
Future plan
The main part of the future work will be depend on
the mixture identification and impurities detection by using different
analysis techniques such as TLS, GC-MS, and NMR to confirm all undesired
products which formed by acetone-acetone reaction. Therefore,
supercritical carbon dioxide as a new technology to purify undesired
products associated with acetone reaction (Dimerization).
Appendix
A. Appendix: The NMR phenomenon
Nuclear Magnetic Resonance (NMR) spectroscopy is a
method of great interest and important for the study of chemical
substance. The use of pulsed Fourier transform methods with spectrum
accumulation made it possible to obtain high resolution spectra (Sander
and Hunter, 1993).
B. The chemical shift1
Resonance occurs at slightly different
frequencies for each type of proton, depending on its chemical binding
and position in a molecule. This variation is caused by the cloud of
electrons about each nucleus, which shields the nucleus against the
magnetic field, thus requiring a slightly lower value of v0to achieve
resonance than for a bare proton (Sanders and Hunter, 1993). Protons
attached to or near electronegative groups such as OH, OR, OCOR, COOR
and halogens experience a lower density of shielding electrons and
resonate at higher v0. Protons farther removed from such groups, as in
hydrocarbon chains, resonate at lower vO.These variations are called
chemical shifts and are commonly expressed in relation to the resonance
of tetra methyl silane (TMS) as zero of reference. The total range of
proton chemical shifts in organic compounds on the order of 10ppm.
For any nucleus, the separation of chemically shifted
resonances, expressed in Hz, are proportional to BO. When expressed in
ppm, as common, the chemical shifts are independent of BO. The
electronic screening of nuclei is actually anisotropic so that the
chemical shift is a directional quantity and depends on the orientation
of the molecule with respect to the direction of the magnetic field. In
solution, the motional
averaging produces an isotropic value of the chemical shift.
C. Nuclear coupling
Nuclei sufficiently removed from each other do not
feel the effects of the magnetic fields of the other nuclei. In this
case, the local magnetic field at each nucleus is essentially equal to
B0. If BO can be made very homogeneous over the sample, the width of the
resonance may be very small.
D. Direct dipole-dipole coupling
In most substances, protons contribute to local
fields and are sufficiently numerous to have a marked effect. The C
atoms also contribute to the local fields, but their natural abundance
is very small, therefore they do not have a visible effect.
E. Indirect nuclear coupling
Magnetic nuclei may transmit information to each
other concerning their spin states not only directly through space, but
also through the intervening covalent bonds. This is indirect or scalar
nuclear coupling, also known a J coupling. Rapid tumbling of the
molecule does not reduce this interaction to zero. If the nucleus has n
sufficiently close, equivalently coupled spin - % neighbors, its
resonance will be split into n+1 spin states of the neighboring group of
spin. Thus one neighboring spin splits the observed resonance to a
doublet, two produce a 1:2:1 triple, three a 1:3:3:1 quarter, and so on.
The strength of the coupling is denoted by a coupling constant J and is
expressed in Hz.
For more articles in Open Access Journal of
Engineering Technology please click on:
https://juniperpublishers.com/etoaj/index.php
Comments
Post a Comment